Today’s construction industry is moving towards digitalization, and model-based construction methodology is at the core of this reform. Steel detailing services are a significant component of this industry, particularly in light of the intricacy of modern structure design. Using a 3D BIM model for steel detailing not only helps in the design documentation but also helps in the documentation required during the manufacturing and construction of the steel members. 3D model-based documentation offers greater accuracy, efficiency, and cost savings than 2D-based documentation. Given the numerous benefits, many professionals still use the conventional 2D documentation method of static drawings because of the comfort zone.
According to a construction technology report by JBKnowledge, analysts have predicted that the number of developers not using BIM has been declining, and the future of the construction industry will be BIM.
Need to shift from 2D CAD to 3D BIM
Traditionally reliant on 2D models, steel detailers, fabricators, and erectors needed precise section cuts and details on design papers. In the 2D-based documentation system, structural engineers use 2D CAD design drawings. These drawings produce general arrangement drawings with floor plans, elevations, cross sections, and details. Construction details like member sizes and installation coordinates are included in these designs. Manual checks and calculations must be performed based on these drawings, resulting in schedule delays, potential errors, and inefficient workflow. Thus, a 3D model-based documentation workflow can be used to enhance the steel detailing capabilities.
3D model-based documentation workflow
A 3D model is created to carry out the design tasks, identify potential flaws, and verify those faults maintaining the design integrity. This approach reduces costs and saves time by integrating manufacturing and on-site processes, which boosts accuracy and efficiency. The Structural BIM Modeling can assist in producing shop drawings, quantity information calculations, and automatic member placement in the factory and on-site. Through task automation, this approach reduces the need for physical labor and conserves raw materials. The manufacturing processes and steel detailing capabilities can be enhanced using this approach. When used in conjunction with 2D drawings, BIM software ensures consistency in production drawings and boosts productivity by linking 3D models, views, and sheets based on objects.
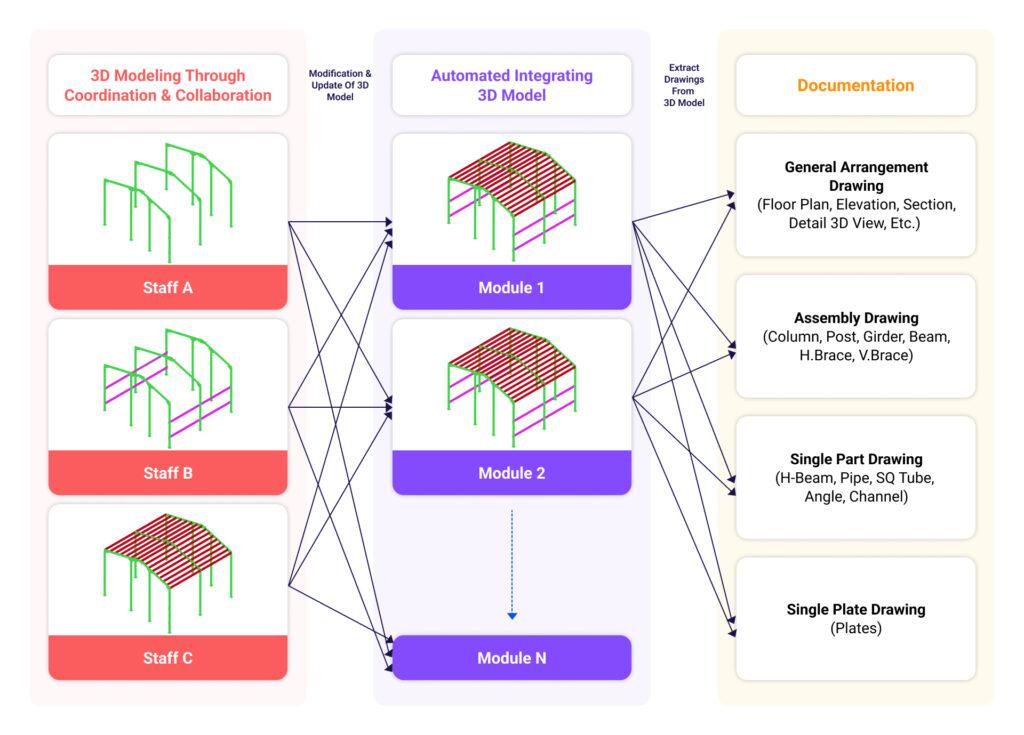
Comparison between 2D and 3D documentation
Fabrication documentation such as general arrangement, assembly, single part, and single plate drawings are created using AutoCAD. To guarantee their integrity, these documents are created on the spot and double-checked. The documentation process for the 2D drawing-based approach is divided into drawing reviews and necessitates collaboration. On the other hand, when comparing 2D drawings without a 3D model, human mistake frequently occurs. Engineers can do 3D modeling for parts or floor connections utilizing steel detailing software, facilitating efficient work. BIM software automatically updates fabrication documents and views by modifying the parametric properties of 3D models. This helps in reducing human errors in documentation processes and saves time.
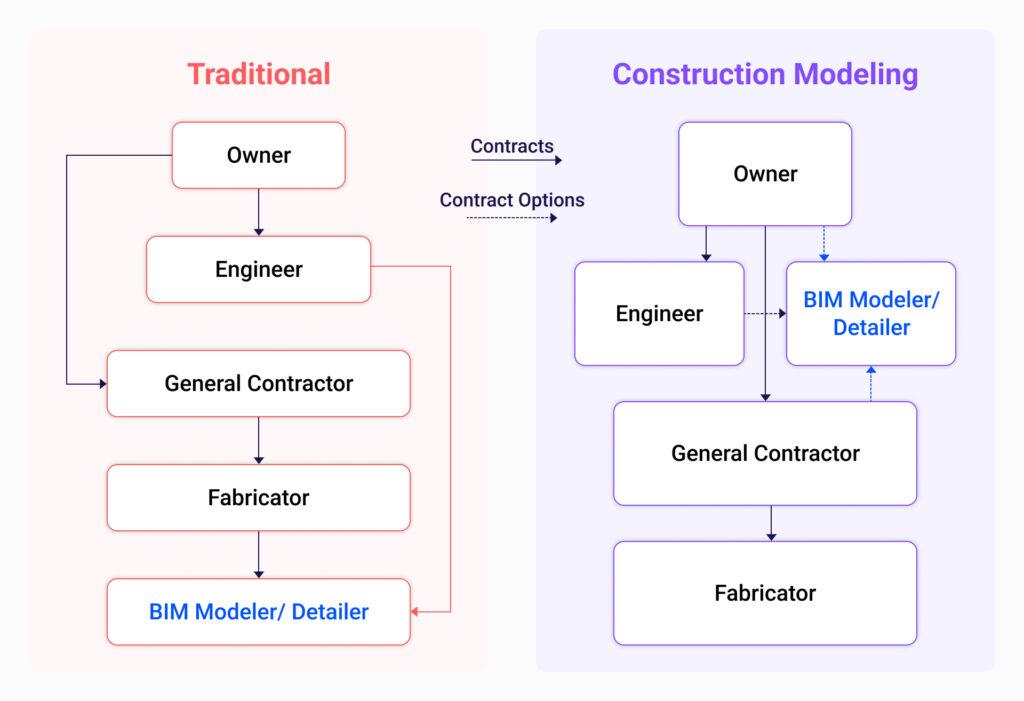
Benefits of using 3D documentation
Structures are more visually represented, fabricators are more competitive, and complete information covering the product development lifecycle is all made possible by 3D workflows. Using 3D technology for steel detailing has the following advantages:
- Increased Scope of Work and Efficiency: Working in 2D restricts possibilities and forces fabricators to employ only 2D documentation drawings. More extensive and complex projects are possible due to the efficiency and competitive advantage of integrating 3D. To stay in business, small steel detailers must adjust to fabricator expectations and provide value in complex projects.
- Automatic Generation of Drawings: A general arrangement (GA) drawing can be made using the 3D structure, including sections, floor plans, side views, anchor bolt designs, and more. 2D drawings for on-site construction can be extracted from the 3D model, improving their accuracy and efficiency. 3D software is parametric, which allows for speedier adjustments and automated reflection in all necessary 2D designs.
- Early detection of errors: Due to a lack of visualization, 2D drawings frequently result in errors; therefore, stakeholders must be creative and consistent. Time, money, and resources are saved during the onsite construction when errors are prevented by 3D technology’s better visualization and conflict detection capabilities.
- Cost Optimization: Misunderstandings, incorrect fabrications, and expensive construction errors might result from using 2D designs. Richly detailed 3D models minimize the risk of financial loss and enhance stakeholder communication, eliminating the need for costly drawings and refabrication.
- Enhanced Detailing Capabilities: When modeling in 3D, 100% accuracy is guaranteed, even for projects with dynamic geometry. But in 2D designs, potential errors like rebars intruding or bar spacing breaches are hard to see. In 3D, intricate rebar detailing can be done faster, mainly when 3D geometry is easily accessible.
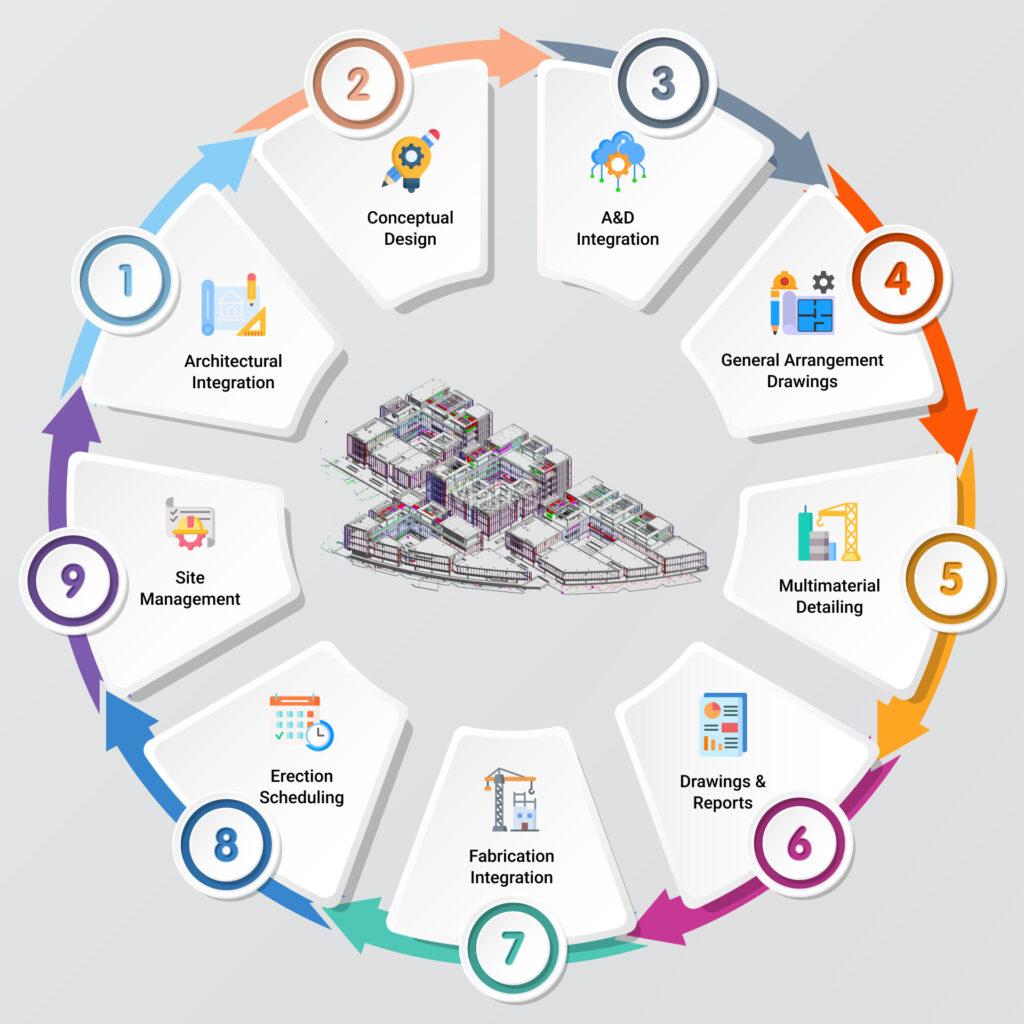
Conclusion
It can be concluded that to stay competitive, modernize its procedures, streamline workflows, and create sustainable steel buildings, the construction sector is adopting new technologies. Several issues, including paperwork, communication breakdowns, shop drawing accuracy, and human data entry errors, can be resolved by combining these technologies with steel detailing processes.